My rear subframe refurbishment
#21

I believe Don B mentions in his photo essay that the dogbones should be tightened
after lifting the wishbone to ride height with a trolley jack.
Probably any bonded rubber bush that changes position in droop should be tightened
while at ride height, whether you lower the car or raise the wishbone.
after lifting the wishbone to ride height with a trolley jack.
Probably any bonded rubber bush that changes position in droop should be tightened
while at ride height, whether you lower the car or raise the wishbone.
#22

since everyone here is focussed on the rear subframe anyways ...
I need to transport one of these in the trunk of a X308 this week.
Please check out this plan:
a) undo the halfshafts at the differential
b) remove front mounting plate
c) remove bottom mounting plate
d) loosen inner pivots of lower wishbones
e) swing lower wishbones up like the wings on a aircraft carrier plane
letting the halfshafts and hubs go inwards whichever way works
f) lay on surface of the differential back cover in trunk
The idea behind swinging the wishbones + halfshafts in is to make the assembly
narrow enough to fit the trunk. I would break it down further, but the seller is
not really interested in having me squat there.
Is this going to work?
What is the distance between the companion flange and the back of the differential.
This represents the max height in the trunk when it is rolled over on the cover.
I need to transport one of these in the trunk of a X308 this week.
Please check out this plan:
a) undo the halfshafts at the differential
b) remove front mounting plate
c) remove bottom mounting plate
d) loosen inner pivots of lower wishbones
e) swing lower wishbones up like the wings on a aircraft carrier plane
letting the halfshafts and hubs go inwards whichever way works
f) lay on surface of the differential back cover in trunk
The idea behind swinging the wishbones + halfshafts in is to make the assembly
narrow enough to fit the trunk. I would break it down further, but the seller is
not really interested in having me squat there.
Is this going to work?
What is the distance between the companion flange and the back of the differential.
This represents the max height in the trunk when it is rolled over on the cover.
#23

Hi plums!
Sounds like a worthy challenge but I have a feeling you can do it, though I don't know if you can do it without detaching the wishbones/control arms.
Good...,
I would suggest bringing an old blanket to protect your rear seat and putting these in the back seat. The bottom plate is as wide as the body of the car, so I doubt it will fit in the trunk with the diff and wishbones.
I suspect this may be difficult to accomplish given how tight Jag trunks are and given how heavy and unwieldy the assmembly will be. Given the solid design of the X300 wishbones, I don't think they would fold far enough upward toward the diff output shafts to do you any good, so they'd have to fold downward to fold compactly enough to have a chance of fitting in the trunk as an assembly.
I weighed the differential of our '93 at 98 pounds. Add the pendulum, wishbone tie and wishbones, and you're probably looking at something like 200 pounds. I would suggest disassembling things to this point, then taking some careful measurements of the assembly and trunk to see if there is any chance it could fit before you make an attempt at lifting it. If the measurements indicate a no go, I think you can just remove the two long fulcrum bolts and the wishbones should detach. Just carefully note the position of any spacer washers, and take photos as you go. Take with you some penetrating oil, a mallet and a long 3/8" socket extension to use as a drift punch in the event one of the fulcrum bolts is corroded and resists being driven out.
I assume you're already planning to leave your spare tire at home.
I believe you can do it! Please let us know how it goes!
Cheers,
Don
Sounds like a worthy challenge but I have a feeling you can do it, though I don't know if you can do it without detaching the wishbones/control arms.
Good...,
b) remove front mounting plate
c) remove bottom mounting plate
c) remove bottom mounting plate
d) loosen inner pivots of lower wishbones
e) swing lower wishbones up like the wings on a aircraft carrier plane
letting the halfshafts and hubs go inwards whichever way work
f) lay on surface of the differential back cover in trunk
e) swing lower wishbones up like the wings on a aircraft carrier plane
letting the halfshafts and hubs go inwards whichever way work
f) lay on surface of the differential back cover in trunk
I weighed the differential of our '93 at 98 pounds. Add the pendulum, wishbone tie and wishbones, and you're probably looking at something like 200 pounds. I would suggest disassembling things to this point, then taking some careful measurements of the assembly and trunk to see if there is any chance it could fit before you make an attempt at lifting it. If the measurements indicate a no go, I think you can just remove the two long fulcrum bolts and the wishbones should detach. Just carefully note the position of any spacer washers, and take photos as you go. Take with you some penetrating oil, a mallet and a long 3/8" socket extension to use as a drift punch in the event one of the fulcrum bolts is corroded and resists being driven out.
I assume you're already planning to leave your spare tire at home.
I believe you can do it! Please let us know how it goes!
Cheers,
Don
Last edited by Don B; 12-01-2014 at 10:17 AM.
#24

Thanks Don!
Your insight is invaluable.
Um ... the spare tire was to remain in the well. With the companion flange facing the
sky and the differential cover resting on the floor, I was hoping there would be enough
depth in the trunk. Assorted old blankets, bungee cord and rope will come along in case
I have to tie the trunk down partially open.
Removing the inner fulcrum pins would be ideal. The problem is whether it is easy
or it becomes a nightmarish struggle while the seller waits to see my car disappear
down the road. He has a home shop and an impact. But at the selling price, is not
too eager to spend much time at this. Completely undertandable.
I'll have another look at your photo albums to see if I can pick up any clues.
Thanks again!
Your insight is invaluable.
Um ... the spare tire was to remain in the well. With the companion flange facing the
sky and the differential cover resting on the floor, I was hoping there would be enough
depth in the trunk. Assorted old blankets, bungee cord and rope will come along in case
I have to tie the trunk down partially open.
Removing the inner fulcrum pins would be ideal. The problem is whether it is easy
or it becomes a nightmarish struggle while the seller waits to see my car disappear
down the road. He has a home shop and an impact. But at the selling price, is not
too eager to spend much time at this. Completely undertandable.
I'll have another look at your photo albums to see if I can pick up any clues.
Thanks again!
#25

I think aside from the difference in the design of the wishbones/control arms, the '95 will be nearly identical to our '93 shown in my photos.
I think if you'll measure your X308 diff from the front of the pinion/input flange to the tips of the rear lower mounting studs, you'll be able to judge how likely the X300 diff will fit in your trunk in the orientation you're envisioning.
Let us know how it goes!
Cheers,
Don
Last edited by Don B; 11-30-2014 at 11:21 PM.
#26

All I can say is that its a very very heavy unit and the inner bolts hinging the wishbones on mine don't want to come loose which results in very limited up-down travel, they certainly can't be folded up which I think is what was suggested.
Maybe if you put carpet on the back of the boot and the sides you could put it nose first in with the wishbones resting on the boot lip, then some bubble wrap and then tie the boot lid down (boot=trunk)
Maybe if you put carpet on the back of the boot and the sides you could put it nose first in with the wishbones resting on the boot lip, then some bubble wrap and then tie the boot lid down (boot=trunk)
#27
#28

I think I will use the knotted wire wheel to de-rust the a-frame.
I had considered getting it shot blasted but decided against it due to keeping the budget down and worries of the blast material getting stuck inside.
Anyway - I have a question which I'm hoping someone can help with -
Where the bolts go through the subframe there are liners including the ones shown below with domed heads.
I think these are alloy or some hard plastic but I'm worried about damaging them with the wire brush as I need to get in there to remove the rust.
Do these come out?
Thanks
I had considered getting it shot blasted but decided against it due to keeping the budget down and worries of the blast material getting stuck inside.
Anyway - I have a question which I'm hoping someone can help with -
Where the bolts go through the subframe there are liners including the ones shown below with domed heads.
I think these are alloy or some hard plastic but I'm worried about damaging them with the wire brush as I need to get in there to remove the rust.
Do these come out?
Thanks

#30

I think I will use the knotted wire wheel to de-rust the a-frame.
I had considered getting it shot blasted but decided against it due to keeping the budget down and worries of the blast material getting stuck inside.
Anyway - I have a question which I'm hoping someone can help with -
Where the bolts go through the subframe there are liners including the ones shown below with domed heads.
I think these are alloy or some hard plastic but I'm worried about damaging them with the wire brush as I need to get in there to remove the rust.
Do these come out?
Thanks
I had considered getting it shot blasted but decided against it due to keeping the budget down and worries of the blast material getting stuck inside.
Anyway - I have a question which I'm hoping someone can help with -
Where the bolts go through the subframe there are liners including the ones shown below with domed heads.
I think these are alloy or some hard plastic but I'm worried about damaging them with the wire brush as I need to get in there to remove the rust.
Do these come out?
Thanks
of the right inner diameter to fit over those nipples, then bolt through the copper
and through the nipples. The copper will shield the nipples. Then finish off the shielded
bits with a flat file instead of the wire brush.
A citric acid bath might be an alternative to wire brushing.
#31
#32

The long inner bolts securing the wishbones either side of the diff didn't want to budge and there was some rust on the middle of the bolts, so as I couldn't detect any wear there I decided (rightly or wrongly) to leave them in place.
So I removed the yoke from front -

Lifted out the diff -

And replaced the yoke giving me access to remove the corrosion ready for painting whilst reducing the weight to something I could lift with one hand and support on my workbench -


The angle grinder and knotted wire wheels removed most of the rust (thanks RD!) and I used smaller wire wheels with an electric drill for the more inaccessible places -

Paint was delivered yesterday (2 part mastic) and I decided on silver as the main colour but will try and overpaint with red and yellow spray cans to bring some bling to the the shocks and springs.
So I removed the yoke from front -

Lifted out the diff -

And replaced the yoke giving me access to remove the corrosion ready for painting whilst reducing the weight to something I could lift with one hand and support on my workbench -


The angle grinder and knotted wire wheels removed most of the rust (thanks RD!) and I used smaller wire wheels with an electric drill for the more inaccessible places -

Paint was delivered yesterday (2 part mastic) and I decided on silver as the main colour but will try and overpaint with red and yellow spray cans to bring some bling to the the shocks and springs.

The following users liked this post:
Don B (08-07-2015)
#33
#35
#36

The bearings feel good and with the diff out I can get to everything to clean and paint so there seemed little point in trying any harder.
"if at first you don't succeed - give up and get yourself a beer"

#37

I purchased all of the pendulum bushes from SNG Barrett not too long ago.
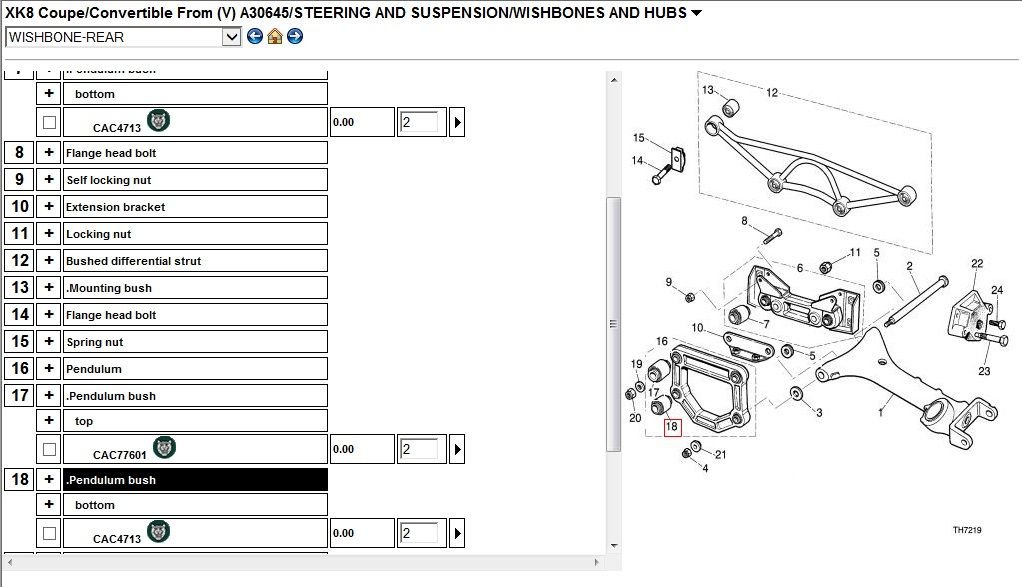
#38

No, I had assumed there must be some sort of bush/bearing on the control arm itself where the pivot bolt goes through it. I have not seen it up close but it now seems that there isn't one. Does the control arm just grind directly on the pivot bolt, or does the pivot bolt rotate with the control arm inside 7 & 17?
#39