Ground Strap - Intermittent Power Loss
#1

Has anyone else had a problem with the ground strap. My problem manifests itself by a periodic loss of all electical power. I have cleaned and tighened all battery connections from both the battery and at the other ends. However periodcally I have a total loss of power which is restored by wiggling the negatove strap. The sprap itself, which is a branded cable, looks brand new and is clean and tigh on the battery. Any one else have this problem. Seems like the solution is just replace the negative strap.
#2

Resistance to electrical flow does not always have visible presence.
a new negative cable wouldn’t hurt and doesn’t cost that much.
there are conductive grease products that help maintain a good connection. The silver based ones are the best, with the copper infused grease a second place. The silver based grease is very pricey (Amazon has it) but my 10 gram tube has last years and is still half full.
Dielectric grease is not a suitable product for this usage in my opinion. It impedes electron flow rather than facilitating it. If it’s used, the current flow is achieved in spite of the use of dielectric grease, not because of it.
Z
a new negative cable wouldn’t hurt and doesn’t cost that much.
there are conductive grease products that help maintain a good connection. The silver based ones are the best, with the copper infused grease a second place. The silver based grease is very pricey (Amazon has it) but my 10 gram tube has last years and is still half full.
Dielectric grease is not a suitable product for this usage in my opinion. It impedes electron flow rather than facilitating it. If it’s used, the current flow is achieved in spite of the use of dielectric grease, not because of it.
Z
#3
#4

Resistance to electrical flow does not always have visible presence.
a new negative cable wouldn’t hurt and doesn’t cost that much.
there are conductive grease products that help maintain a good connection. The silver based ones are the best, with the copper infused grease a second place. The silver based grease is very pricey (Amazon has it) but my 10 gram tube has last years and is still half full.
Dielectric grease is not a suitable product for this usage in my opinion. It impedes electron flow rather than facilitating it. If it’s used, the current flow is achieved in spite of the use of dielectric grease, not because of it.
Z
a new negative cable wouldn’t hurt and doesn’t cost that much.
there are conductive grease products that help maintain a good connection. The silver based ones are the best, with the copper infused grease a second place. The silver based grease is very pricey (Amazon has it) but my 10 gram tube has last years and is still half full.
Dielectric grease is not a suitable product for this usage in my opinion. It impedes electron flow rather than facilitating it. If it’s used, the current flow is achieved in spite of the use of dielectric grease, not because of it.
Z
On your second point, I beg to disagree. There are conductive greases available usually using silver or carbon as the conductive material. However, these are expensive and are produced for very specialised applications, none of which normally apply to conventional cars, and can do more harm than good.
Anti-seize grease, which is cheap and widely used in automobile application, is usually copper or aluminium based but is dielectric (non-conducting) and for electrical uses is a poor choice compared to silicone grease or even bearing grease or vaseline.
The point of dielectric grease is to fill the gaps between the conducting surfaces so that moisture and damp air cannot enter and cause increased resistance over time due to metal to metal corrosion. A moisture and air impenetrable grease which does not dry out is required which is why silicone grease excels in this application.
There is no requirement for conductive grease, which will always be a poor second to direct metal to metal contact, so all the "heavy lifting" will still be done by actual terminal to terminal contact, even where conductive grease is used.
Conductive grease is less resistant to moisture penetration and corrosion promotion than silicone grease and therefore is not only more expensive but is less effective in performing the primary function.
Of course, we must all be allowed to make our own choices and that is a good thing. 👍
Richard
#5

I prefer the conductive grease because it ensures these old connections have the best chance at being 100% effective. The power line transmission industry uses a copper and carbon based grease products. The electronic industry uses the silver based grease product. I’m not against “borrowing” good ideas when see them for limited automotive uses.
To be sure, one must take care not to use too much. Which might make a conductive path to somewhere undesired.
I use the dielectric grease on rubber parts like spark plug boots and rubber light sockets. But never on metals.
those are my choices that have been working very well for 5 decades.
My right could very well be someone else’s wrong.
If applying gobs of grease on electrical parts is a persons modus operandi, or “MO”, then my strategy would be less successful.
Z
To be sure, one must take care not to use too much. Which might make a conductive path to somewhere undesired.
I use the dielectric grease on rubber parts like spark plug boots and rubber light sockets. But never on metals.
those are my choices that have been working very well for 5 decades.
My right could very well be someone else’s wrong.
If applying gobs of grease on electrical parts is a persons modus operandi, or “MO”, then my strategy would be less successful.
Z
Last edited by zray; Today at 09:31 AM.
#6

Hi aeginc77,
It does sound as though you battery negative ground cable may have an internal corrosion or connection problem. Have you disconnected the cable at the body end, cleaned the body, eyelet terminal, bolt and washer, and reassembled? You can connect an ohmmeter to each end of the ground cable to measure its resistance, which should be 0 ohms or very close, then flex and manipulate the cable to see if the resistance changes.
It could also be possible that your problem is in the High Power Protection Module, which is the plastic box on the trunk forward bulkhead where the megafuses are mounted. Perhaps while wiggling the negative cable you are also moving the positive cable and affecting its connection at the module? An important periodic maintenance procedure is to take all the megafuses out, clean their blades, the threaded studs, washers and nuts, then reassemble. I use a small brass bristle brush and CRC Electronic Contact Cleaner spray.
I don't think this is your problem, but for others reading your thread, I solved a similar problem of intermittent loss of electrical power in our X308 by replacing all the Ignition Positive relays and the EMS Control Relay. You can find the locations of these relays in the Electrical Guide, which you can download at jagrepair.com, courtesy of motorcarman who provided the files and Gus who hosts the site. If you shop around, you can find suitable Bosch relays.
In addition to cleaning the High Power Protection module, it's also great periodic maintenance to clean all the battery power connections at all the fuse boxes, false bulkhead, starter, alternator, both ends of the engine ground strap, and every ground point you can access. It only takes a little corrosion to add considerable resistance to the circuit, and all the resistance points in the circuit are cumulative. You can find the locations of all the battery power and ground locations in the Electrical Guide.
I agree with Richard that the best electrical connection is gas-tight bare metal against bare metal, so I do not use so-called "conductivity enhancing" products. All you have to do is research the resistance of these "conductive grease" products compared to bare copper, silver, gold and aluminum to see that these greases increase the resistance of a connection. They are probably fine in high-power industries, but I worked in the music recording industry for nearly 40 years and have a lot of experience in the high-end audio/audiophile world, where small signal integrity is paramount and where these sorts of products have been touted and debated for decades. Most of the top recording and mastering engineers I know prefer clean, dry, gas-tight metal-on-metal connections with no added "enhancer." For connections that are exposed to the elements, like the engine ground strap, I assemble them clean and dry, then spritz them with CRC Battery Terminal Protector or wipe some dielectric grease on the outside of the nut/stud/eyelet terminal assembly to help protect against water ingress.
Also, for others reading this thread, the ignition switch is a potential suspect. This is the electrical switch that fits on the end of the key lock barrel. You can test the switch at its connector inside the steering column cowl. The Electrical Guide shows which contacts should conduct in each switch position.
Cheers,
Don
It does sound as though you battery negative ground cable may have an internal corrosion or connection problem. Have you disconnected the cable at the body end, cleaned the body, eyelet terminal, bolt and washer, and reassembled? You can connect an ohmmeter to each end of the ground cable to measure its resistance, which should be 0 ohms or very close, then flex and manipulate the cable to see if the resistance changes.
It could also be possible that your problem is in the High Power Protection Module, which is the plastic box on the trunk forward bulkhead where the megafuses are mounted. Perhaps while wiggling the negative cable you are also moving the positive cable and affecting its connection at the module? An important periodic maintenance procedure is to take all the megafuses out, clean their blades, the threaded studs, washers and nuts, then reassemble. I use a small brass bristle brush and CRC Electronic Contact Cleaner spray.
I don't think this is your problem, but for others reading your thread, I solved a similar problem of intermittent loss of electrical power in our X308 by replacing all the Ignition Positive relays and the EMS Control Relay. You can find the locations of these relays in the Electrical Guide, which you can download at jagrepair.com, courtesy of motorcarman who provided the files and Gus who hosts the site. If you shop around, you can find suitable Bosch relays.
In addition to cleaning the High Power Protection module, it's also great periodic maintenance to clean all the battery power connections at all the fuse boxes, false bulkhead, starter, alternator, both ends of the engine ground strap, and every ground point you can access. It only takes a little corrosion to add considerable resistance to the circuit, and all the resistance points in the circuit are cumulative. You can find the locations of all the battery power and ground locations in the Electrical Guide.
I agree with Richard that the best electrical connection is gas-tight bare metal against bare metal, so I do not use so-called "conductivity enhancing" products. All you have to do is research the resistance of these "conductive grease" products compared to bare copper, silver, gold and aluminum to see that these greases increase the resistance of a connection. They are probably fine in high-power industries, but I worked in the music recording industry for nearly 40 years and have a lot of experience in the high-end audio/audiophile world, where small signal integrity is paramount and where these sorts of products have been touted and debated for decades. Most of the top recording and mastering engineers I know prefer clean, dry, gas-tight metal-on-metal connections with no added "enhancer." For connections that are exposed to the elements, like the engine ground strap, I assemble them clean and dry, then spritz them with CRC Battery Terminal Protector or wipe some dielectric grease on the outside of the nut/stud/eyelet terminal assembly to help protect against water ingress.
Also, for others reading this thread, the ignition switch is a potential suspect. This is the electrical switch that fits on the end of the key lock barrel. You can test the switch at its connector inside the steering column cowl. The Electrical Guide shows which contacts should conduct in each switch position.
Cheers,
Don
Last edited by Don B; Today at 12:32 PM.
The following users liked this post:
XJRay (Today)
#7

Thanks for the input Don. I have cleaned the cables including where the positive attaches to the HTTP and used electrical contact cleaner. I suspect that there is problem in that braided ground strap and I will replace it with an actual cable. Just a question related to your comment on the ignition switch. If that was faulty would I lose ALL electrical power. When I lose power I mean everything.No lights, no radio nothing. I don't even have to put key in the switch. I open the door and no lights come on and can immeidately tell I've got a no power situation.
Alan
Alan
Trending Topics
#8

Hi aeginc77,
“…..so I do not use so-called "conductivity enhancing" products. All you have to do is research the resistance of these "conductive grease" products compared to bare copper, silver, gold and aluminum to see that these greases increase the resistance of a connection. ….”
“…..so I do not use so-called "conductivity enhancing" products. All you have to do is research the resistance of these "conductive grease" products compared to bare copper, silver, gold and aluminum to see that these greases increase the resistance of a connection. ….”
with all due respect, I believe my own eyes before I give any credibility to internet sources.
I test each connection for resistance after using a silver based grease. There is zero resistance when measured by a quality mutilmeter, a Fluke 117.
Conversely, before the silver grease was employed, these same connections all showed varying levels of resistance. Which was expected given the age of these connections..
Z
#9

Thanks for the input Don. I have cleaned the cables including where the positive attaches to the HTTP and used electrical contact cleaner. I suspect that there is problem in that braided ground strap and I will replace it with an actual cable. Just a question related to your comment on the ignition switch. If that was faulty would I lose ALL electrical power. When I lose power I mean everything.No lights, no radio nothing. I don't even have to put key in the switch. I open the door and no lights come on and can immeidately tell I've got a no power situation.
I mentioned the ignition switch for the sake of others who may find your thread because they are also dealing with intermittent power loss. I do think your symptoms suggest a problem with battery power. The Body Processor Module receives its primary power from Fuse 7 in the driver's side fuse box, which should always be live regardless of the position of the ignition switch. I don't think a bad ignition switch would prevent the BPM from illuminating the interior lighting when the door is opened.
Cheers,
Don
#10

with all due respect, I believe my own eyes before I give any credibility to internet sources.
I test each connection for resistance after using a silver based grease. There is zero resistance when measured by a quality mutilmeter, a Fluke 117.
Conversely, before the silver grease was employed, these same connections all showed varying levels of resistance. Which was expected given the age of these connections..
I test each connection for resistance after using a silver based grease. There is zero resistance when measured by a quality mutilmeter, a Fluke 117.
Conversely, before the silver grease was employed, these same connections all showed varying levels of resistance. Which was expected given the age of these connections..
When I mentioned researching the resistances of conductive greases, I certainly was not referring to general "internet sources." I was referring to the manufacturers' own data sheets. As an example, here is a chart from MG Chemicals, a manufacturer of several conductive greases:
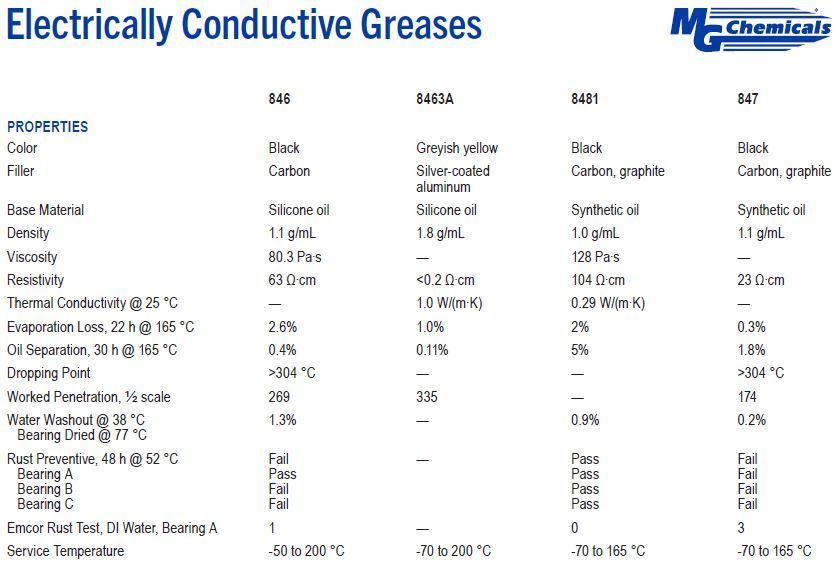
By far, the lowest-resistance grease they offer contains silver-coated aluminum filler, and its resistance is specified as <0.2 ohms-centimeter. This is very low for a conductive grease. However, it is greater than zero, which is the resistance between two clean, dry metal surfaces. Which is why I prefer clean, dry, gas-tight connections.
As I mentioned earlier, all the added resistances in a circuit are cumulative, so if we add, say, 0.05 ohm to every connection with silver grease, pretty soon we've added a few tenths of an ohm to the circuit, which is enough to throw off the signals of precision sensors like the MAFS, ECTS, etc.
The Fluke 117 is an excellent meter, but my recollection is that, like most hand-held DMMs, it only measures to one-tenth of an ohm. If so, it would not be a suitable instrument for measuring the added resistance of a silver-bearing conductive grease to only one connection. On the other hand, it might be able to detect the difference when using a carbon-bearing conductive grease, but the resistivity of carbon greases is far too high to ever consider using in automotive systems (the MG carbon greases are rated at 23 ohms-cm, 63 ohms-cm and 104 ohms-cm).
Aside from superconductors in which electrical resistance disappears at some critical temperature (like absolute zero), I do not know of any substance that would not add resistance when applied to an electrical connection.
Cheers,
Don
Last edited by Don B; Today at 07:29 PM.
#11

Don,
thank you for the detailed information. If I ever have any conductivity issues I will clean off the terminals coated in the silver based grease.
If a metal to metal connection is tightened securely do you think the grease only fills the microscopic voids ? Or do you surmise that the grease has a few microns thickness across all the terminal area that otherwise would be making 100% metal to metal contact.
I go with the former assertion. The grease is filling the voids and irregularities in the metal that otherwise would be conducting zero current. Where the metal is making full contact the grease is forced out by the tightening process.
all theory of course. I’ll certainly report back in on this subject if I have any conductivity anomalies.
Z
thank you for the detailed information. If I ever have any conductivity issues I will clean off the terminals coated in the silver based grease.
If a metal to metal connection is tightened securely do you think the grease only fills the microscopic voids ? Or do you surmise that the grease has a few microns thickness across all the terminal area that otherwise would be making 100% metal to metal contact.
I go with the former assertion. The grease is filling the voids and irregularities in the metal that otherwise would be conducting zero current. Where the metal is making full contact the grease is forced out by the tightening process.
all theory of course. I’ll certainly report back in on this subject if I have any conductivity anomalies.
Z
The following users liked this post:
Don B (Today)
#12

That is a great question that has been pondered over the years in various industries and forums. My own theory is that in a "scraping" connection like a bayonet-base light bulb, the grease may be mostly pushed away from the bayonet contact points but remain in the surrounding areas to help seal out water.
But in "squashing" connection, as in a ground stud with eyelet terminals and washers secured by a nut, a thin layer of grease may remain over the entire contact area, at its thinnest areas still many molecules thick. And if there are multiple wires connected at the same stud, there may be a thin layer of grease between every pair of terminals and washers, so the effect is cumulative. As far as my own personal logic goes, the only way to eliminate this possibility is to not put grease between the connectors, but only on the outside of the assembly after the nut is torqued.
Cheers,
Don
The following users liked this post:
XJRay (Today)
Thread
Thread Starter
Forum
Replies
Last Post
iramphal
XJ6 & XJ12 Series I, II & III
14
08-28-2024 10:56 PM
Craig Nelson
E type ( XK-E )
2
06-18-2015 11:58 AM
Currently Active Users Viewing This Thread: 2 (0 members and 2 guests)